6-8 November 2025
KTPO Convention Centre,
Whitefield, Bengaluru
The Growing Importance of Robotics in Warehousing
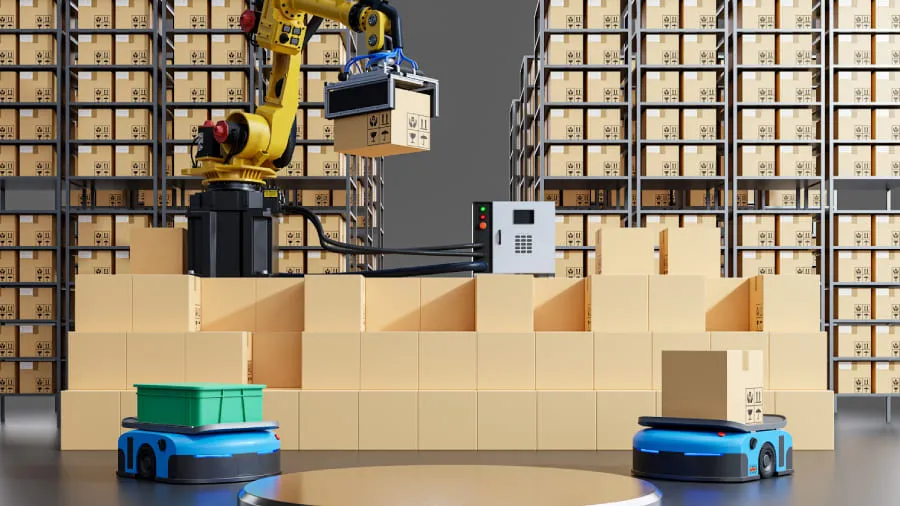
Robots have been used in manufacturing for decades, but their integration into warehousing is more recent. As logistics operations become more complex and businesses strive to improve efficiency, robotics is playing a critical role in automating repetitive tasks, optimizing workflows, and reducing errors. In fact, the global warehouse robotics market is expected to grow significantly, reflecting its increasing importance to the industry.
Key Applications of Robotics in Warehousing
Robots are versatile tools that can be deployed in various warehousing tasks. Here are some of the most common applications:
1. Automated Picking and Packing
- Robotic Arms: Automated picking systems, often equipped with robotic arms, are designed to locate and pick items from shelves or bins. Using advanced sensors and AI, these robots can identify items with precision and speed, greatly enhancing order fulfillment processes.
- Collaborative Robots (Cobots): Cobots work alongside human workers, taking over repetitive tasks like packing and labeling, while humans handle more complex or value- added tasks.
2. Autonomous Mobile Robots (AMRs)
- AMRs are intelligent robots that move goods within the warehouse without the need for fixed infrastructure like conveyor belts. Guided by sensors, maps, and machine learning algorithms, AMRs can transport products from one part of the warehouse to another, optimize routes, and avoid obstacles, leading to improved workflow efficiency.
3. Automated Storage and Retrieval Systems (AS/RS)
- AS/RS solutions use robotic cranes or shuttles to automatically store and retrieve items from designated storage locations. These systems are ideal for high-density storage environments, maximizing the use of available space and reducing the time it takes to fulfill orders.
Inventory Management
- Robots equipped with cameras and sensors can scan barcodes and RFID tags to update inventory records in real-time, reducing the need for manual stock-taking. This level of automation helps reduce human errors, ensuring that inventory levels are accurate and up- to-date.
Material Handling
- Forklifts and other heavy-duty robots are used for moving pallets, heavy loads, and raw materials across the warehouse. Autonomous forklifts and pallet movers can operate 24/7, improving material flow and reducing downtime.
Join the Future of Warehousing
Robotics is transforming warehousing as we know it. From increasing productivity to enhancing operational efficiency, robotic solutions are helping businesses meet the demands of modern supply chains. Don’t miss your chance to explore these innovations firsthand at the Intralogistics & Warehousing Expo—the leading platform to source robotics solutions that will elevate your warehouse operations to the next level.